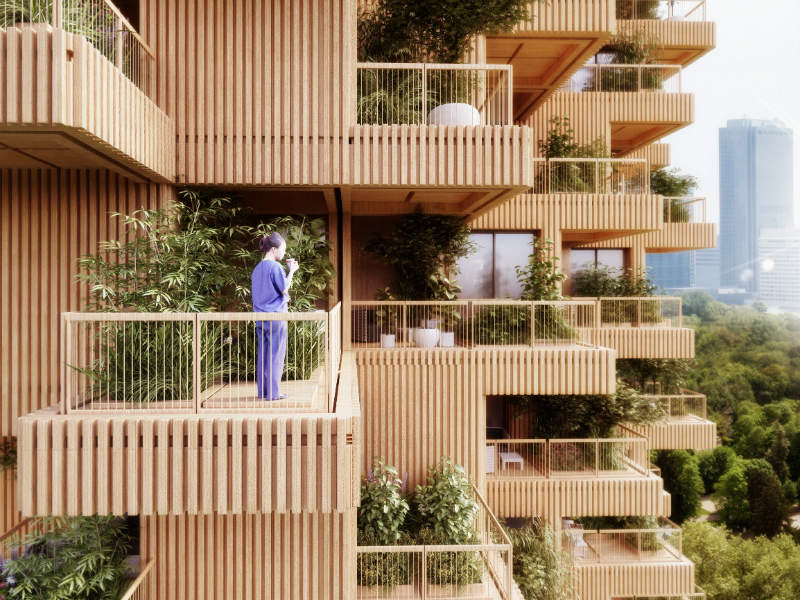
Toronto’s Tree Tower: A Green Oasis in the City
When startup architectural firm Penda won Architizer’s A+ Award in 2016 for ‘Emerging Firm of the Year’ the team was already developing the ‘Tree Tower Toronto’. Sustainable, efficient to construct and designed with city dwellers’ health in mind, Penda hopes this wooden 18-storey tower will act as a catalyst for future high-rise buildings.
Penda has partnered with CLT (Cross Laminated Timber) consultants Tmber to design and deliver this modular, 62m high building. It offers a 4,500-square metre residential area and 550 square metres of public space, which includes a café, a children’s day-care centre and community workshop areas.
“Our cities are an assembly of steel, concrete and glass,” says Chris Precht, partner at Penda. “The warm, natural appearance of wood and the plants growing on its facade bring the building to life and that could be a model for environmentally-friendly developments and sustainable extensions of our urban landscape.”
Buildings against construction pollution
By building with wood, Penda’s goal is to set a successful residential building precedent that would reduce pollution caused by the construction industry.
“The construction industry is using almost half of all energy created on our globe and are we are a big contributor to the pollution of our environment,” says Precht. “Buildings are using up sites and resources of our surroundings and I believe buildings can be and do more than that.”
Today more than 80% of people living in urban areas are exposed to air quality levels that exceed the World Health Organization (WHO) limits. Reports show that 30% of global greenhouse gas emissions are attributable to buildings and currently the construction industry in the UK creates 32% of landfill waste and as much as 50% in the USA. In Canada waste from construction, renovation and demolition has increased by over 30% between 2000 and 2010.
How well do you really know your competitors?
Access the most comprehensive Company Profiles on the market, powered by GlobalData. Save hours of research. Gain competitive edge.

Thank you!
Your download email will arrive shortly
Not ready to buy yet? Download a free sample
We are confident about the unique quality of our Company Profiles. However, we want you to make the most beneficial decision for your business, so we offer a free sample that you can download by submitting the below form
By GlobalData“As architects we shouldn’t just think about how to make our buildings more beautiful or more efficient, but we need to design healthier buildings for vital cities,” says Precht. “Creating more public spaces in them, producing energy for the surrounding or growing food for the neighbourhood.”
Canada: a history of modular and wooden buildings
With a long tradition of wood construction and a pioneering country for vertical wooden structures, Canada was the ideal location to develop a modular wooden high-rise. In order to promote sustainable developments, the government in Canada awards credits of up to 20% in funding for buildings that exceed carbon footprint standards.
Canada is also a country with a world first in prefabricated modular construction, and in 1967 it opened Moshe Safdie’s Habitat 67 in Montreal, Quebec. Its intention was to be a new model for inner-city living; instead of small flats in soaring high-rise blocks, it provided house-like accommodation that included small gardens and differing vantage points.
Habitat 67 was constructed from 354 prefabricated modules, which were stacked and linked by steel cables. A project that never reached it potential – its overall size was reduced by the government and was thus more expensive than planned – it presented a new way to consider compact living in urban environments.
“Inspired by Habitat 67, the Tree Tower is using a modular building process, where pre-fabricated and pre-cut CLT panels are assembled to modules off-site at an indoor facility,” says Chris, adding that while building modular is nothing new these days, building modular with individuality and variety takes it to a new level.
“After the work on site, with foundation, ground floor and a base core done, all modules including fixtures and finishes are delivered to the site and craned into place,” he adds. “During the process of stacking the modules, the timber clad facade panels are installed and sealed.”
Chris explains that by going fully modular and prefab, the process is faster, less noisy, reduces waste and allows for a high degree of quality control as most parts of the building are assembled in a controlled indoor environment.
“The structure of the building is mainly massive timber panels with a hybrid of CLT, concrete and steel elements, where needed, and can be seen as a prominent statement to use engineered wood products in vertical structures,” he adds.
Yet as inspiring as Safdie’s Habitat 67 is, the building later allegedly encountered issues with damp after water crept into the concrete in certain places. Chris explains that the extensive processes the wood goes through means the wood would be protected from any similar issues from occurring.
An example for future ecological cities
“What I love most about building with solid wood panels is that on one hand wood is a natural and low-tec material, but on the other hand the process of engineering Cross Laminated Timber panels is highly technological and mechanical,” he says. “Due to a sophisticated assembly-line and CNC-milling, all details of the parts and the connection of them is very precise (in contrast to concrete).”
He adds: “Despite a precise building process and engineered details, it’s crucial to protect wood from water. Once the prefabricated elements are put into place, the building is treated as any other conventional construction. A layer of water-protection is applied onto the building and a water-proofed cladding mounted on its facade.”
While Precht says that Penda is currently in the “schmerzlich [painful] phase” of the project, the company is trying to start the approval process in 2018.
“We hope the building could be an example of a more ecological future in our cities,” he says. “To misuse a JFK quote, the question shouldn’t be what a city can do for a building, but what a building can do for a city, and I hope the Toronto Tree Tower can be an example for that.”